
以下圖文由一木編輯 這期接著為大家分享五金壓鑄件的知識,,上期分享的內(nèi)容由于截圖上傳后看不清楚,,這期盡量以文字版本呈現(xiàn),總數(shù)字在八千字以內(nèi),,內(nèi)容有點長,,可以先收藏或者轉(zhuǎn)發(fā)朋友圈,待有時間了再復(fù)讀,。 以下為正文:
【一】冷隔 缺陷現(xiàn)象: 溫度較低的金屬流互相對接但未熔合而出現(xiàn)的縫隙, 呈不規(guī)則的線形, 有穿透的和不穿透的兩種, 在外力的作用下有發(fā)展的趨勢,。 
產(chǎn)生原因: 金屬液澆注溫度過低或模具溫度過低。 合金成分不符合標準, 流動性差,。 金屬液分股填充, 熔合不良,。 澆口不合理, 流程太長。 填充速度低或排氣不良,。 壓射比壓偏低,。 脫模劑用量過多。
分析判斷與解決對策: 產(chǎn)品發(fā)黑, 伴有流痕, 適當提高燒注溫度和模具溫度,。 改變合金成分, 提高流動性,。 燙模件看鋁液流向, 金屬液碰撞產(chǎn)生冷隔出現(xiàn)一般為渦旋狀, 伴有流痕, 改進澆注系統(tǒng), 改善內(nèi)澆口的填充方向, 另外可在鑄件邊緣設(shè)集渣包以改善填充條件。 伴有遠端填壓不實, 更改澆口位置和截面積, 改善排溢條件, 增大溢流量,。 產(chǎn)品發(fā)暗, 經(jīng)常伴有表面氣泡, 提高壓射速度,。 鑄件整體壓不實, 提高比壓(盡量不采用)。
【二】擦傷&拉傷 缺陷現(xiàn)象: 順著脫模方向, 由于金屬粘附, 模具制造斜度太小而造成鑄件表面的拉傷痕跡,嚴重時成為拉傷面甚至產(chǎn)生裂紋,。 
產(chǎn)生原因: 型芯, 型壁的鑄造斜度太小或出現(xiàn)倒斜度,。 型芯, 型壁有壓痕。 合金粘附模具,。 鑄件頂出偏斜或型芯軸線偏斜,。 型壁表面太粗糙。 涂料常噴涂不到,。 鋁合金中含鐵量低于0.6%,。 合金澆注溫度高或模具溫度太高。 澆注系統(tǒng)不正確,直接沖擊型壁或型芯,。 填充速度過快,。 型腔表面未氮化,。
分析判斷與解決對策: 產(chǎn)品一般拉出亮痕, 不起毛。修正模具, 保證制造斜度,。 產(chǎn)生拉毛甚至拉裂, 打光壓痕,。更換型芯或焊補型壁。 拉傷起毛,。拋光模具。 單邊大面積拉傷, 頂出時有異音,。修正模具,調(diào)整或更換頂桿,,使頂出力平衡。 拉傷為細條紋, 多條,。打磨拋光表面,。 模具表面過熱,均勻粘鋁。涂料用量薄而不勻,不能漏噴涂料,。 型腔表面粘附鋁合金,。適當增加含鐵量到0.6%-0.8%。 型腔表面粘附鋁合金,尤其是內(nèi)澆口附近,。降低澆注溫度和控制模具溫度在工藝要求范圍內(nèi),。 型壁或型芯粘附鋁嚴重。調(diào)整內(nèi)澆口的位置與填充方向,。 模具型腔內(nèi)澆口處沖涮嚴重并伴有粘附合金,。適當降低速度。 型腔表面經(jīng)常粘附合金,。必須進行模具表面氮化處理,。
【三】欠鑄 缺陷現(xiàn)象: 金屬液未充滿型腔,鑄件上出現(xiàn)填充不完整的部位,。多出現(xiàn)在鑄件末端或狹窄深腔處,。 
產(chǎn)生原因: 合金流動不良引起: 金屬液含氣量高,氧化嚴重,,以致流動性下降,。 合金澆注溫度及模具溫度過低。 內(nèi)澆口速度過低,。 蓄能器內(nèi)氮氣壓力不足,。 壓室充滿度低,比壓低,。 鑄件壁太薄或厚薄懸殊等設(shè)計不當,。
澆注系統(tǒng)不良引起: 澆口位置、導(dǎo)流方式,、內(nèi)澆口股數(shù)選擇不當,。 內(nèi)澆口截面積太小,。
排氣條件不良引起:
排氣不暢。 涂料過多,,未被烘干燃盡,。 模具溫度過高,型腔內(nèi)氣體壓力較高,,不易排出,。
分析判斷與解決對策: 改善合金的流動性: 產(chǎn)品內(nèi)部質(zhì)量不好,表面氣泡多,。精煉合金液,,盡可能排除氣體及非金屬夾雜物。 伴有冷隔,、流痕,。適當提高合金澆注溫度和模具溫度。 產(chǎn)品表面出現(xiàn)小凹坑,,欠鑄周圍伴有冷隔,。適當提高壓射速度。 壓力表有緩沖現(xiàn)象且顯示數(shù)值不符合工藝要求,,鑄件伴有壓不實現(xiàn)象,。補充氮氣,提高有效壓力,。 鑄件表面有冷金屬痕跡,,同時存在壓不實現(xiàn)象。調(diào)整壓室直徑,,提高壓射比壓,,采用定量澆注。 壁薄處欠鑄周圍存有明顯的冷隔或壓不實,。河改進鑄件結(jié)構(gòu),,適當調(diào)整壁厚,另外可開設(shè)輔助澆口,。
改進澆注系統(tǒng): 欠鑄前端伴有冷隔,、融合不完整現(xiàn)象。根據(jù)填充模擬或?qū)嶋H燙模件選擇澆口位置,、導(dǎo)流方式幾澆口股數(shù),。 經(jīng)常伴有粘內(nèi)澆口現(xiàn)象。增大內(nèi)澆口截面積或提高壓射速度,。 改善排氣條件,。 產(chǎn)生欠鑄處周圍顏色黑,伴有雜質(zhì)堆積及氣泡等。增設(shè)溢流槽和排氣道,,深凹腔處可采用頂桿間隙或型芯間隙排氣,。 表面顏色不亮、流痕嚴重,。涂料使用薄而均勻,,吹干燃盡后合模。 經(jīng)常伴有粘模多,,拉傷嚴重,,表面氣泡。降低模具溫度至工藝規(guī)定范圍,。
【四】氣孔 缺陷現(xiàn)象: 壓室,、澆道和型腔內(nèi)的氣體卷入制件內(nèi)部形成的形狀較為規(guī)則,表面較為光滑的孔洞,。 
產(chǎn)生原因: 模具溫度太高,開模過早,。 填充速度太高,,金屬流卷入氣體過多。 涂料發(fā)氣量大,,用量過多,,澆注前未燃盡,使揮發(fā)氣體被包在鑄件表層,,另涂料含水量大,。 型腔內(nèi)氣體沒有排出,排氣不順,。 合金熔煉溫度過高,。 鋁合金液體除氣不徹底,吸有較多氣體,,鑄件凝固時析出留在鑄件內(nèi) 填充時產(chǎn)生紊流,。
分析判斷與解決對策: 測溫槍測試模具表面溫度,顯示數(shù)值超過工藝規(guī)定范圍,。降低模具表面溫度,,增加保壓時間。 鑄件表面內(nèi)澆口壓入的金屬流明顯比其它部位亮很多,。填充速度高產(chǎn)生原因一方面是設(shè)備本身的壓射速度高,,另一方面可能是內(nèi)澆口太薄造成。降低壓射速度,,適當增加內(nèi)澆口厚度,。 判斷內(nèi)澆口薄的方法:是否有澆口易粘現(xiàn)象,,降低二快速度看遠端是否有嚴重壓不實現(xiàn)象,,不給壓打件,,看是否有多股鋁液流,。 噴涂時察看霧的顏色是否呈白色,合模前察看型腔是否還有氣體殘留,。更換涂料或增大涂料與水的配比,。 在燙模階段,鑄件表面有明顯的漩渦和涂料堆積,。判斷及解決方法:調(diào)開檔,,人為產(chǎn)生漲模,如果解決,,需開排氣道,。 鑄件表面內(nèi)澆口壓入的金屬流特別亮并伴有粘結(jié)。適當降低澆注溫度,。 取樣塊測密度,,看是否符合要求。重新進行除氣處理或在保溫爐內(nèi)進行再次精煉,。 燙模階段鑄件表面明顯有各流溶接不到一起的痕跡伴有涂料堆積,。判斷及解決方法:涂黑油生產(chǎn),看痕跡是否有堆積,,分析堆積部位,,解決方法,a,,開設(shè)或加大相應(yīng)部位的集渣包,,b,調(diào)整內(nèi)澆口流向,、位置或填充方向,。
【五】縮孔 缺陷現(xiàn)象: 壓鑄件在冷凝過程中,由于內(nèi)部補償不足所造成的形狀不規(guī)則,,表面較粗糙的孔洞,。 
產(chǎn)生原因: 合金液澆注溫度過高。 制件結(jié)構(gòu)壁厚不均勻,,產(chǎn)生熱結(jié),。 溢流槽容量不夠,溢口太薄,。 脫模劑用量過多,。 模具的局部溫度偏高。 內(nèi)澆口較小,。 澆注壓力小,,速度慢。 合金液成分不合理。
分析判斷與解決對策: 鑄件局部表面特亮,。遵守合金熔煉規(guī)范,,合金液過熱時間不能太長,降低澆注溫度,。 壁厚處易出現(xiàn)凹陷,,同時伴有冷隔、壓不實現(xiàn)象,。與客戶技術(shù)工程師協(xié)商,,在不影響使用功能的前提下,改進鑄件結(jié)構(gòu),,消除金屬積聚部位,,均勻壁厚,緩慢過渡,。設(shè)備條件允許的情況下,,采用二次擠壓是有效的辦法。 鑄件表面存在壓不實現(xiàn)象,。適當提高比壓,。 溢流槽附近的鑄件表面存有涂料和冷金屬積聚的痕跡。加大溢流槽容量,,增厚溢流口,合理選擇溢流口位置,。 鑄件局部表面有疊層現(xiàn)象,,內(nèi)澆口斷面有壓不實和疏松現(xiàn)象。提高壓室充滿度,,采用定量澆注,,控制料餅的厚度。 鑄件表面發(fā)黑,,壓不實,,有冷隔。適當改善澆注系統(tǒng),,增大內(nèi)澆口截面積,,以利壓力很好地傳遞。 模具測溫槍檢查模具局部區(qū)域,??刂颇>呔植繙囟冗_到溫度平衡,必要時增設(shè)點冷卻,。噴涂局部高溫區(qū)時時間長些,,達到冷卻目的。
【六】夾渣 缺陷現(xiàn)象: 鑄件基體內(nèi)存在有硬度高于金屬基體的細小質(zhì)點或塊狀物,使加工困難,,刀具磨損嚴重,,加工后鑄件上常常顯示出不同亮度的硬質(zhì)點。 
產(chǎn)生原因: 合金中混入或析出比基體金屬硬的金屬或非金屬物質(zhì),,如AL2O3及游離硅等 由鋁,、鐵、錳,、硅組成的復(fù)雜化合物,,主要上由MnAL3在熔池較冷處形成,然后以MnAL3為核心使Fe析出,,又有硅等參加反應(yīng)形成化合物,,游離硅混入物。 合金液與耐火磚,、涂料產(chǎn)生反應(yīng)的生成物,。 金屬料不純,含有其它異物,。合金料粘附油污,,工具不清潔。 金屬硬質(zhì)點,,混入未溶解的硅元素原料,,混入促進初生硅結(jié)晶生長的原料,混入生成金屬間化合物結(jié)晶的物質(zhì),。 偏析性硬質(zhì)點,。由于急冷組織致密化,使容易偏析的成分析出成為硬質(zhì)點,。 合金液在保溫爐內(nèi)放置時間太長,。 保溫爐下部的合金液長時間沒有清除,產(chǎn)生積淀,。
分析判斷與解決對策: 分析判斷:該缺陷由于在鑄件內(nèi)部,,肉眼無法觀察。另外X-光探傷無法識別,,只能通過加工能辨別出是何種性質(zhì)的硬質(zhì)點,。 熔煉時要減少不必要的攪動和過熱,保持合金液的純凈,,鋁合金液長期在爐內(nèi)保溫時,,應(yīng)周期性精煉去氣,澆鑄時不要把合金液表面的氧化物舀入勺內(nèi),,熔化工具上的氧化物必須清除,,熔化工具上的涂料不能與鋁產(chǎn)生反應(yīng),。 鋁合金中含有鈦、錳,、鐵等組元時,,應(yīng)勿使偏析并保持潔凈,用干燥的精煉劑精煉,,但在鋁合金含有鎂時,,要注意補償。 鋁合金中含銅,、鐵量多時,,應(yīng)使含硅量降低到10.5%以下,適當提高澆注溫度以避免使硅析出,。 使用不和鋁反應(yīng)的耐火磚,、涂料,定期更換爐襯,。 嚴加管理爐料,,不允許混有異物或異種材料,回爐料不允許粘有油污,、砂及塵土等,。工具上的鐵銹及氧化物及時清除。 調(diào)整合金成分,,不能直接加硅元素,,要用中間合金。熔煉溫度要高,,時間要長,,使硅充分溶解。加料時防止合金錠使熔融合金凝固,。盡可能減少促進初生硅易于生長的成分。減少溫度波動范圍,,不要使合金的溫度過高或過低,。控制產(chǎn)生金屬化合物的材料的含量,,如有要在高溫下熔煉,。控制溫度波動范圍,,使合金處于熔融狀態(tài),。 當合金澆入壓室后,應(yīng)立即壓射填充,。盡可能不含有Ca,、Mg,、Na等易引起急冷效應(yīng)的合金成分,Ca應(yīng)控制在0.05%以下,。 長時間放置在保溫爐內(nèi)的合金液必須掏出重新熔煉,,盡可能做到隨用隨和料。 按工藝規(guī)定及時掏出保溫爐下部的合金液,,重新加入新的合金液,。
【七】脆性 缺陷現(xiàn)象: 鑄件基本金屬晶粒過于粗大或細小,使鑄件易斷裂或碰碎,。 
產(chǎn)生原因: 合金液過熱過大或保溫時間過長,。 激烈過冷,結(jié)晶過細,。 鋁合金中雜質(zhì)鋅,、鐵等含量太多。 鋁合金中含銅量超出規(guī)定范圍,。 熔化工具涂料層脫落,。
分析判斷與解決對策: 熔化爐和溫控爐溫控系統(tǒng)監(jiān)控。合金不宜過熱,,避免長時間保溫,。 依據(jù)模具型腔溫度場模擬分析,找出溫度變化差別大的區(qū)域,,增設(shè)點冷卻或點加熱,,提高模具溫度,降低澆注溫度,。 通過光譜分析檢查合金化學(xué)成分,。嚴格控制合金中鋅、鐵的含量,。 通過光譜分析檢查合金化學(xué)成分,。嚴格控制合金中銅的含量。 保持熔化工具涂料層完整良好,。
【八】滲漏&漏壓 缺陷現(xiàn)象: 壓鑄件經(jīng)試驗產(chǎn)生漏水,、漏氣或滲水。干式壓力試驗機紅燈亮 
產(chǎn)生原因: 增壓壓力不足,。 澆注系統(tǒng)設(shè)計不好,。 (1)距滲漏區(qū)較遠,內(nèi)部質(zhì)量差,; (2)金屬流融合不好,,產(chǎn)生冷隔; (3)內(nèi)澆口截面積小,,增壓傳遞不到位,,遠端形成氣孔或縮松等,。 合金選擇不當,流動性差,、不適合壓鑄生產(chǎn),。 排氣不良,局部產(chǎn)生氣孔,、縮松和冷隔等缺陷,。 鑄件設(shè)計不合理,壁厚不均勻或過厚,,存在熱結(jié),,產(chǎn)生氣孔、縮松縮裂等嚴重影響氣密性的缺陷,。 加工量大,,破壞表面氧化致密層或使壁厚變薄,尤其雙面加工部位 合金熔煉溫度過高,,保溫時間長,,壓鑄時壁厚處易產(chǎn)生縮松和縮裂 涂料發(fā)氣量大,易產(chǎn)生氣孔,。 壓力檢驗設(shè)備故障,。 密封面有損傷或不符合粗糙度要求。如加工面有劃傷,、壓痕等,。非加工密封槽因龜裂引起粗糙度差等。 鑄件變形引起密封面翹曲,。
分析判斷與解決對策: 件遠端或壁厚處壓不實,。提高比壓。 可根據(jù)模擬填充或?qū)嶋H樣件調(diào)試分析判斷,。合理改進澆注系統(tǒng),。 選用良好合金。 在燙模階段分析鑄件局部是否存在卷氣,、合金流融合不好,。合理增設(shè)集渣包和排氣道。 采用X-光探傷找出熱結(jié)處,。如該熱結(jié)確實是滲漏點,,則可與客戶工程師協(xié)商更改該處結(jié)構(gòu),,減小壁厚,。另外還可以采用二次擠壓的工藝解決熱解處的滲漏。 盡量避免加工或采用盡可能小的加工余量,。 X-光探傷檢查鑄件內(nèi)部質(zhì)量,。適當降低熔煉溫度,。 X-光探傷檢查鑄件內(nèi)部質(zhì)量。用發(fā)氣量小的涂料,。 鑄件進行浸漬處理,。 利用合格鑄件鑒定壓力試驗設(shè)備。維修檢驗設(shè)備,。 通過打壓試驗即可發(fā)現(xiàn),。加強過程保護,及時維修模具,。 平面度檢查可發(fā)現(xiàn),。控制生產(chǎn)過程,,保壓時間必須足夠,。防止工序運轉(zhuǎn)過程中擠,壓,,摔等,。
【九】針孔現(xiàn)象A 缺陷現(xiàn)象: 壓鑄件內(nèi)部存在細小孔洞,很多情況下是成片出現(xiàn),,X-光探傷不容易被發(fā)現(xiàn),,只有在加工表面上可以看見。 
產(chǎn)生原因: 爐料不干凈,,帶含有氣體的雜質(zhì),,尤其是返回料的使用。 熔煉溫度過高,,致使合金液吸氣,。 精煉、除氣后的合金液保持時間過長,。 散流充型時空氣或潤滑劑的氣體產(chǎn)物進入金屬,。 金屬熔化過程中氣體的析出。 模具型腔排氣效果差,。 模具溫度過高,,合金液充型后冷凝速度慢。 合金流填充的狀態(tài)不合理,,形成紊流,,使氣體進入合金。
分析判斷與解決對策: 使用干凈清潔的爐料,。對于返回料和廢品件,,必須分級使用,不合格的料要經(jīng)過處理后才能使用,。 察看熔化爐溫度控制顯示表,;必須使熔化溫度控制工藝要求范圍內(nèi),。 處理好的合金液盡可能及時使用,不能在熔化爐或保溫爐內(nèi)放置時間過長,,長時間存放的合金液必須經(jīng)過重新處理后方可使用,。 在散流充型時盡量增大金屬流速度。減小壓室直徑,、減小內(nèi)澆口截面積或增大壓射速度,。 通過密度檢測儀分析金屬液中的含氣量。熔化爐中合理精煉,,出爐后除氣徹底,。 增大排氣槽的截面積,鑄件周圍合理設(shè)置溢流槽,。 合理設(shè)計模具冷卻系統(tǒng),,通過整體模具的冷卻增加合金液的凝固速度。 合理設(shè)計內(nèi)澆口的位置,、方向和截面積,,保證金屬流連續(xù)填充并達到順序凝固。
【十】針孔現(xiàn)象B 缺陷現(xiàn)象: 鑄件表面上呈現(xiàn)松散不緊實的宏觀組織,。內(nèi)部存在材質(zhì)不致密區(qū)域,,同時伴有縮 孔。X-光探傷時可以被發(fā)現(xiàn)但有些模糊,。 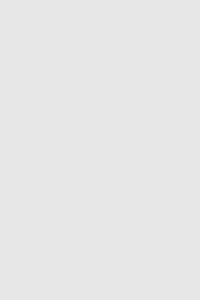
產(chǎn)生原因: 合金收縮大,,多出現(xiàn)在厚大部位,即合金體積收縮過大,。 鑄件上存在劇烈過渡,,如由薄壁處直接過渡到厚大深腔處,且過渡圓角較小,。 增壓壓力不夠,。 壓鑄機增壓建立晚,持壓時間短或持不住壓,。 模具型腔溫度過高,。 合金液澆注量少,即料餅太薄,,增壓無法傳導(dǎo),。 涂料噴涂過多。 合金澆注溫度低
分析判斷與解決對策: 可能的情況下更換合金牌號,。鑄件盡可能減少厚大部位,。 調(diào)整鑄件結(jié)構(gòu),劇烈變化處必須圓滑過渡。 鑄件表面即可發(fā)現(xiàn)壓不實現(xiàn)象,。提高增壓壓力。 檢修壓鑄機,,保證增壓,。 利用測溫槍檢測模具型腔各部位的溫度。整體模具平衡設(shè)置點冷卻和線冷卻,。局部高溫區(qū)多噴涂,,進行強制冷卻。 采用定量澆注,。料餅必須控制在工藝規(guī)定范圍,。 涂料噴涂均勻而薄。 適當提高合金澆筑溫度,。
【十一】漲模 缺陷現(xiàn)象: 壓射過程完成后模具打開時,,在分型面(非型腔部位)產(chǎn)生一定厚度的飛邊,直 接影響鑄件的尺寸,。有時飛邊處于液態(tài)情況下在壓射過程直接由分型面或滑動拼 接處濺出,。 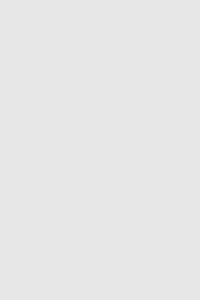
產(chǎn)生原因: 合模前,模具分型面不干凈,,粘有殘鋁或其它粘附物,。 動,定模在調(diào)整合模時不嚴密,,間隙較大,。 壓鑄機鎖模力不夠。 壓鑄模具動,、靜把模面不平行,。 壓鑄機4根鎖模大杠應(yīng)力不均。 壓射壓力很大,,嚴重超出工藝要求范圍,。 滑動拼接鑲塊間隙變大。 側(cè)抽滑塊閉鎖失效,,使滑塊產(chǎn)生后退,。 壓鑄機安裝模具型板不平行,可能是型板本身問題,,也可能是大杠與導(dǎo)套的間隙過大,。 壓射比壓變大,可能更換直徑小的料杯或壓射夜里突然增大,。
分析判斷與解決對策: 查看模具分型面,,漲模狀態(tài)不是四個方向。清除分型面任何粘附物,保證合模前分型面干凈,。 查看合模時曲拐的狀態(tài),,漲模狀態(tài)是四個方向較均勻。在分型面清理干凈的情況下,,向前調(diào)整合模,。 通過理論計算加上一定的保險系數(shù),可以發(fā)現(xiàn)壓鑄設(shè)備鎖模力是否合適,,漲模狀態(tài)基本是四方均勻,。更換噸位大的壓鑄設(shè)備。在保證產(chǎn)品質(zhì)量的前提下,,減少澆排系統(tǒng)的面積,。 在保證模具分型面清潔、干凈的情況下,,著色配研模具(在壓鑄機上進行),,通常情況下是分型面的局部著不上色或著色較輕。卸下模具利用平臺和高度尺檢查動,、靜把模面的平行度,。如平行度不合格,維修模具,。 在第4條檢查工作的情況下,,如果模具檢查平行度合格,則考慮調(diào)整壓鑄機大杠的應(yīng)力情況,。 查看設(shè)備壓射壓力表,,漲模狀態(tài)基本是四方均勻。降低壓射壓力,。 滑動拼接配合處清理干凈的情況下,,用塞尺檢查其間隙。更換或維修鑲塊,。 在側(cè)抽配合處清理干凈的情況下,,著色研配。維修或更換閉鎖快,。 首先確認模具動,、靜把模平面平行,其次確認4根大杠應(yīng)力平均,,壓鑄時可能從一側(cè)或一角跑鋁,,產(chǎn)生漲模。維修設(shè)備,。 漲模的狀態(tài)是四方均勻出現(xiàn)較大飛邊,。更換會原料杯、采用大噸位壓鑄機。保持壓射壓力穩(wěn)定,。
【十二】化學(xué)成分不符合要求 缺陷現(xiàn)象: 經(jīng)光電光譜和金相顯微鏡分析,,鑄件合金元素不符要求或雜質(zhì)太多。 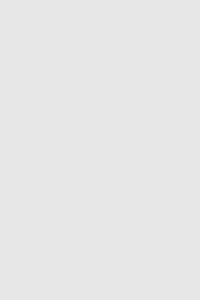
產(chǎn)生原因: 合金錠或原料入廠就存在成分不合格或不準確,。 合金錠或原料金相分析雜質(zhì)多,。 回爐料沒經(jīng)過處理和分析及即投入使用,加入的比例太多,。 試樣的抽取或處理方法不對。 熔煉工藝不當,,如溫度過高,,燒損嚴重,致使某種合金元素的含量發(fā)生變化,。 合金保溫時間太長或保溫爐下半部合金液沒有按要求清爐,,造成沉積使鑄件產(chǎn)生夾雜。另外也可造成某種合金成分含量產(chǎn)生變化,。 熔煉工具沒有刷涂料或涂料剝落,。
分析判斷與解決對策: 合金錠及原料入廠前光譜檢查。返回供貨廠家,; 合金錠及原料入廠前金相檢查,。返回供貨廠家; X-光探傷或斷口分析,。嚴格遵守回爐料的使用管理規(guī)定,; 嚴格執(zhí)行試樣的選取操作方法,正確拋光待檢面,。必要時再次取樣進行復(fù)檢,。在生產(chǎn)中要定期對鑄件進行工藝性試驗; 及時進行光電光譜分析和金相檢查,。嚴格控制合金熔煉溫度和澆注溫度,,盡量消除合金形成氧化物的各種因素; 按工藝要求及時掏爐和清爐,; 嚴格執(zhí)行熔化工具使用操作規(guī)程,。
【十三】機械性能不符合要求 缺陷現(xiàn)象: 鑄件合金的強度、硬度,、延伸率等不符合標準,。主要體現(xiàn)在加工和裝配使用 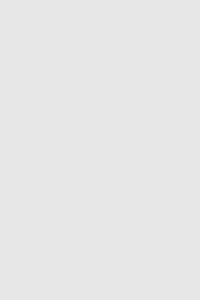
產(chǎn)生原因: 合金化學(xué)成分不符標準。 硬度低:Si,、Cu,、Ni和Zn含量低。 強度低:Si、Ni,、Mn和Cr含量低,。 韌性差:Si、Mg,、Zn等含量高,。 切削性能差:Si、Cu,、Ca含量低,。 鑄件內(nèi)部有氣孔、縮孔,、夾渣和疏松等鑄造缺陷,。 對試樣處理方法不對等。 鑄件結(jié)構(gòu)不合理,,限制了鑄件達到標準,。 熔煉工藝不當,產(chǎn)生氧化物和其它化合物,。
分析判斷與解決對策: 配料熔化要嚴格控制化學(xué)成分,,使其在標準要求范圍內(nèi),最好靠近中值,。 嚴格遵守熔煉,、壓鑄工藝,避免和減少內(nèi)部缺陷,。 按要求做試樣,,在生產(chǎn)中要定期對鑄件進行工藝性試驗。 改善鑄件結(jié)構(gòu),,盡可能避免內(nèi)部應(yīng)力集中,,保證圓滑過渡。 嚴格控制合金熔煉溫度和澆注溫度,,盡量消除合金形成氧化物的各種因素,。
【結(jié)語】 1,以上所有總結(jié)參數(shù)與信息,,僅供參考,,具體還是要以實際產(chǎn)品出發(fā)。 2,,有不清楚,,不明白的地方,歡迎留言,,或者進群討論,,一木非常歡迎,。 3,上兩期的文章點下面的超級鏈接進入: A,五金壓鑄件表面處理工藝詳解
B,結(jié)構(gòu)設(shè)計師對于鋁的認識四(鋁合金壓鑄) 自從跟大神級別混在一起以后,,一木開始淪為正式的小編了,,不過做這樣有深度的技術(shù)含量的小編,還是很樂意的,,同時歡迎各大神繼續(xù)支持本小號,,歡迎來稿分享。 下面再來2份壓鑄成型現(xiàn)場視頻,,加深印象: 建議在WIFI情況下觀看 建議在WIFI情況下觀看
如有錯誤歡迎點擊下方↓留言吐槽批評.
以上所有圖文素材歸原創(chuàng)作者所有,,如有侵犯其它原創(chuàng)者,請后臺聯(lián)系,,可刪,。
|